Magnetic ballast in use will be under the impact of high-voltage pulse . Starter fluorescent lamp ballasts are exposed repeatedly beating the impact of its own self-induced emf , high intensity discharge lamp ballasts, internally triggered exposed to the impact of self-induced emf . Foreign -triggered flip-flops are exposed to high voltage pulses. Each lamp startup process , the ballast winding layers and inter-turn have to withstand much higher than the supply voltage of the voltage pulse . Small power inductive fluorescent lamp ballasts used wire diameter smaller and more turns . Enameled film thickness is proportional to the diameter , fluorescent lamp ballasts used in type Ⅱ enameled Even so, the film thickness of only 1-1.5 Simi . And the prevalence of enameled copper wire drawing industry bigger glitch , copper partial core , low voltage resistance per unit thickness paint thinner and other factors make the enameled surface insulation weak point ( commonly known as the pinhole ) a lot . The ballast windings wound in and will inevitably lead to the phenomenon of stretching and scratching the paint . These factors all contributed to the ballast layers and inter-turn under high pressure in the instantaneous short circuit risks. If the winding shorted turns is large ( commonly known as acute short ) tend to blow the lamp filament without the risk of security failures. Short laps when there are fewer ( commonly known as chronic short ) , lamp starter and ballast can work, but due to other internal short-circuit current is larger circle will soon heat, the polymer film insulation fell so short extent constantly expand , creating a vicious cycle. This case, since the formation of an arc discharge within the lamp , the lamp current is significantly increased even though it is not open. This phenomenon is the result of overheating ballasts ranging since softened plastic fasteners in heavy ballast caused by falling under the action of the phenomenon , wounding hurt things , will cause the ballast weight and the surrounding combustible smoke fire, the formation of fire and fire, seriously compromising security . In the production of ballast products, as long as there is one thousandth of this phenomenon will seriously affect the incidence of corporate reputation and sales, if the incidence of one percent , then, given the quality of their products is notorious . Therefore, despite the inductive ballast failure rate was significantly less than electronic ballasts, but a problem occurs it is often fatal .
To solve this problem , we recommend using the following two methods. First, using the string into the thermal fuse approach. According to the transformer principle known , although partial short circuit current of up to ten times the circle to the current value of the work several times , but the line at the current value increase was not much , because ballast preheat current is generally operating current of 1.3-1.5 times , such as use current fuse can not be smaller operating current . So into the line of the string into the current fuse approach can not be achieved after a short fuse and reliable protection purposes . After the temperature of the windings due to short working hours than normal temperatures rise significantly , into the line can be used in series with the thermal fuse approach. After using the windings shorted to the heat generated by the thermal fuse circuit, so as to achieve the shorted ballast failure does not produce security purposes . This method is known that the fail-safe in a foreign country . In a variety of small appliances imported almost all power transformers using this method . Using this method should pay attention to the following aspects: ① optional thermal fuse current should be allowed to pass reliably than the actual current through it in order to avoid too much current through thermal effects caused by the additional affect its operating temperature . Thermal fuse operation temperature should be selected to be significantly higher than the ballast lamp does not start abnormal operating conditions , the thermal equilibrium temperature , it can avoid the ballast windings not shorted , but when the lamp is in an abnormal malfunction . Suggested the use of the range of motion of 180-195 ℃ thermal fuse . Thermal fuse is installed in addition to the necessary electrically insulating dielectric outer ( Average Thickness 0.03-0.05mm), should be close to the heat source ( winding ) , do not , or by a thick medium to transfer heat through the air , or easily cause thermal fuse when the action or action discrete great problems with their achieve its proper role as insurance .
Another way to solve the magnetic ballast circuit for ballast before dipping semi- insulating paint used more than five times the power supply voltage frequency, and five times the impact test or with continuous pulse generation high-voltage pulse test , which excluded the interlayer between turns poor insulation of semi-finished products , and preferably be able to test the product after vacuum impregnation way . Through the above measures can guarantee the basic product does not produce short circuit ballast . NOTE: The above is not a traditional ballast impact test conductor between the shell and iron high pressure tests. It is about the 1100V high voltage across the winding directly to the ballast and the action time. If you directly to the nominal frequency high voltage is applied across the ballast will definitely make too much current flowing through it do not meet the purpose of simulation , so only through the high- voltage frequency increased to at least five times the power frequency to achieve simulation test , the inverter can be used in actual use the method or methods used to obtain air generators used in this test suitable test power .
Fluorescent ballast abnormal state , due to the starter circuit across the lamp redness caused by the phenomenon , but does not start and end of lamp life when used to transmit a cathode half-wave rectification effect caused by insufficient ballast phenomenon the safe use of some effect . The former state, the ballast is always in the preheating current through the state, the latter is because the operation of the starter repeated intermittently in the ballast through the preheating current state and the way through a half -wave pulse current state. In both cases, the ballast fever is much higher than the normal working hours . Therefore, energy-saving electric dare ballast design and lighting ballast weight injection molded components to withstand heat issues should be considered , should ensure that the ballast is in an abnormal state and to achieve long-term thermal equilibrium so that the heat generated may not bearing injection molded parts produced detrimental to the safety of thermal variations . Enterprises in the design of injection molding material selection should be carried out simulation test in order to ensure safety under abnormal conditions .
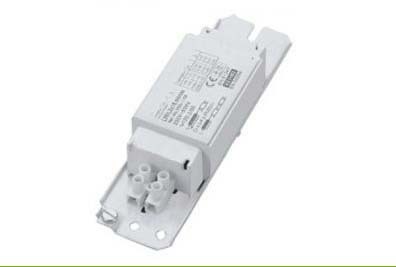